齿轮加工中,材料硬度与平齿机刀具的匹配关系直接影响加工效率、刀具寿命及齿轮精度,需从材料特性、刀具选型和工艺参数三方面综合优化。
1. 材料硬度分类及刀具匹配原则
齿轮材料按硬度可分为三类:
- 低硬度材料(HRC<30):如未热处理的20CrMnTi、45#钢等,适合高速钢(HSS)刀具。此类材料切削阻力小,HSS刀具兼具韧性与经济性。
- 中高硬度材料(HRC30-50):如调质处理的40Cr、42CrMo,需选用硬质合金刀具(如YG8、YW2)。硬质合金硬度达HRA89-93,耐磨性优异,可承受较高切削温度。
- 超高硬度材料(HRC>50):渗碳淬火齿轮(如20CrNiMo)或粉末冶金件,需采用涂层硬质合金(TiAlN涂层)或立方氮化硼(CBN)刀具。CBN硬度仅次于金刚石,耐高温达1400℃,可加工HRC60以上材料。
2. 刀具选型关键技术
- 涂层技术:TiN/TiCN涂层可提升刀具表面硬度20%-30%,Al₂O₃涂层耐热性优异,适用于高速干切。
- 几何参数优化:加工高硬度材料时,采用负前角(-5°~-10°)增强刃口强度,后角6°-8°减少摩擦,螺旋角30°-45°改善排屑。
- 抗冲击设计:对断续切削工况(如斜齿轮加工),选择细晶粒硬质合金或增韧具,提升抗崩刃能力。
3. 工艺参数协同控制
- 切削速度:硬质材料宜采用中低速(80-150m/min),避免热软化效应导致刃口粘连。
- 冷却策略:高硬度齿轮加工推荐高压内冷(压力>7MPa),有效降低切削区温度并辅助断屑。
- 进给量匹配:HRC>45时,进给量需控制在0.05-0.1mm/r,避免刀具过载。
实际应用中,需结合齿轮批量、精度要求(如ISO 6-8级)及设备刚性动态调整。例如,批量生产渗碳齿轮时,采用CBN刀具配合微量润滑(MQL)工艺,可提升加工效率3-5倍,同时实现Ra0.8μm的表面粗糙度。定期检测刀具磨损(VB值<0.3mm)是保证加工稳定性的关键。
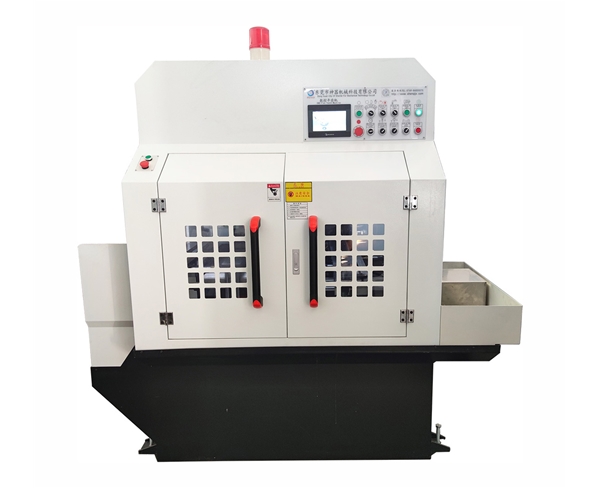
下一条:没有了